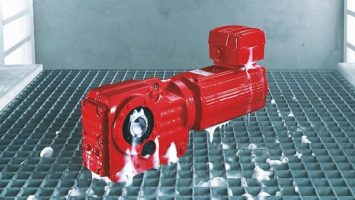
< Previous Sew Eurodrive products | Products index | Next Sew Eurodrive products >
Options for MOVIDRIVE B
Type designation | |
Keypad DBG60B | Standard keypad for parameterization, data management, startup, and diagnostics |
Encoder interfaces DEH11B | – Motor encoder connection: TTL, RS422, sin/cos and HIPERFACE encoders – Distance encoder connection: TTL, RS422, sin/cos and HIPERFACE encoders |
DER11B | – Motor encoder connection: Resolver – Distance encoder connection: TTL, RS422, sin/cos and HIPERFACE encoders |
DEH21B | – Motor encoder connection: TTL, RS422, sin/cos and HIPERFACE encoders – Distance encoder connection: SSI absolute encoder |
DEU21B | – Motor encoder connection: TTL, HTL, RS422, sin/cos, HIPERFACE, SSI, CAN, EnDat 2.1 encoders – Distance encoder connection: TTL, HTL, RS422, sin/cos, HIPERFACE, SSI, CAN, EnDat 2.1 encoders |
DIP11A | – Motor encoder connection: TTL, RS422, sin/cos and HIPERFACE encoders – Distance encoder connection: SSI absolute encoders |
DIP11B | – Distance encoder connection: SSI absolute encoder – Extension of digital inputs and outputs: 8 x inputs, 8 x outputs |
Fieldbus connection – DFE32B / DFE33B – DFE24B – DFP21B – DFC11B / DFD11B – DFI11B / DFI21B – DFS11B / DFS21B | – PROFINET IO / Modbus TCP + EtherNet/IP™ – EtherCAT – PROFIBUS DPV1 – CANopen / DeviceNet™ – INTERBUS / INTERBUS-FOC – PROFIsafe via PROFIBUS / PROFIsafe via PROFINET |
MOVISAFE safety monitor – DCS31B – DCS21B + DFS12B – DCS21B + DFS22B | Safe movement/position monitoring, safe inputs and outputs up to PL e according to EN ISO 13849-1 and – for “safe motion/position monitoring” – for “safe movement/position monitoring and communication” (PROFIsafe/PROFIBUS) – for “safe movement/position monitoring and communication” (PROFIsafe/PROFINET) |
Extension for inputs and outputs – DIO11B | 8× digital inputs and 8× digital outputs; 1 x analog differentiation; 2 x analog outputs |
MOVI-PLC controller – DHE21B/DHE41B – DHF21B/DHF41B – DHR21B/DHR41B – External option: UHX71B | – MOVI-PLC advanced, Ethernet interface – MOVI-PLC advanced, Ethernet / PROFIBUS / DeviceNet™ interface – MOVI-PLC advanced, Ethernet / PROFINET/ Modbus TCP / EtherNet/IP™ interface – Compact controller: - MOVI-PLC power: IEC-61131-3 programmable motion and logic controller or - CCU power: parameterizable application controller |
Other – DRS11B – USB11A – UWS21B | – Synchronous operation card – Interface adapter for connection to a PC via USB interface – Interface adapter for connection to a PC via RS232 interface |
Engineering software MOVITOOLS MotionStudio | The MOVITOOLS MotionStudio program package allows you to conveniently start up, configure and run diagnostics for MOVITRAC B frequency inverters and MOVIDRIVE B application inverters. |
Regenerative power supply MOVIDRIVE MDR60A 15 kW – 160 kW MOVIDRIVE MDR61B 160 kW – 315 kW | The regenerative power supply can supply multiple units with power using a central line connec- tion. In regenerative mode, the power is fed back into the supply system. Using MDR60A/MDR61B saves energy and reduces installation work. |
Braking resistors type BW | BW series braking resistors are available for regenerative operation of the MOVITRAC B frequency inverters and MOVIDRIVE B drive inverters. Using an integrated temperature sensor, the resistor can be protected without external monitoring. |
Line choke type ND | ND series line chokes increase the overvoltage protection of inverters. This is an important characteristic in rough industrial power supply systems, especially if the inverter is installed near a supply transformer. |
Line filter type NF | The NF line filter series is available for EMC-compliant installation according to EN 61800-3. They suppress interference emission on the line side of inverters. These line filters ensure that limit value class C1 is maintained on the supply end. |
Output choke type HD | HD series output chokes suppress interference emitted from unshielded motor cables. They enable the motor to meet limit value class C1 requirements in accordance with EN 61800-3 in EMC-compliant installations. Output chokes provide an alternative to shielded motor cables in EMC-compliant installations. |
Output filter type HF | HF series output filters are sine filters that smooth out the output voltage of inverters. Output filters are used for group drives to suppress discharge currents in motor cables and for long motor cables to prevent voltage peaks. |
06
6.1 Control cabinet installation
MOVIAXIS multi-axis servo inverters
Features – Multi-axis servo system for highly dynamic applications up to 250 A motor current
– Power supply and regenerative power supply up to 187 kW
– DC link power supply for DC 24 V
– Capacitor and buffer module
– Connection of all common motor and distance encoders
– Fieldbus interfaces, fieldbus gateways and clock-synchronized interfaces
– Scaled motion and logic controller directly at the axis system, speed control, positioning, motion control and kinematics
– Wide range of accessories: Cables, braking resistors, line filters, line chokes, brake control units
Power supply module type
Line connection V | 3× AC 380 – 500 |
Nominal power kW | 10, 25, 50, 75 kW at 250% for 1 s |
Block-shaped power supply and regenerative power supply module
Line connection V | 3× AC 380 – 500 |
Nominal power kW | 50, 75 at 250% for 1 s |
Sinusoidal power supply and regenerative power supply module
Line connection V | 3× AC 380 – 480 |
Nominal power kW | 50, 75 at 200% for 1 s |
DC link power supply unit
Supply | Directly from DC link |
Nominal power | 3× 10 A, limited to 600 W total power |
Axis modules
Output current A at 8 kHz | 2, 4, 8, 12, 16, 24, 32, 48, 64, 100 at 250% for 1 s |
Communication interfaces | PROFIBUS, EtherCAT |
Encoder interfaces motor encoder | Hiperface, Resolver, TTL, sin/cos, Endat 2.1 |
Encoder interfaces distance encoder | Hiperface, TTL, HTL, sin/cos, Endat 2.1, SSI |
safety Functional safety | – MXA80 without integrated functional safety – MXA81: Safe Torque Off (STO) up to cat. 3 according to EN 954-1 and PL d to EN ISO 13849-1 – MXA82: Safe Torque Off (STO) up to cat. 4 according to EN 954-1 and PL e to EN ISO 13849-1 – Optional MOVISAFE UCS..B safety module: Drive safety functions (SLS, SDI, SLP, etc.) according to EN 61800-5-2 |
06
Master module
Communication gateway | DeviceNetTM, Profibus, Profinet, EtherNet/IPTM, Modbus TCP |
Data management | Via memory card, automatic data set download when replacing the axis module |
Integrated motion controller | Programmable in IEC 61131, parameterizable functionalities |
6.1 Control cabinet installation
Accessories and options for MOVIAXIS
Encoder and distance encoder card XGH11A | – Multi-encoder card for motor and distance encoder Hiperface, Endat 2.1, sin/cos – Incremental encoder simulation – ± 10 V analog input – DC 24 V supply |
Encoder and distance encoder card XGS11A | – Like XGH11A, additional for SSI encoders |
Input/output card XIA11A | – 4 DI, 4 DO – 2AI, 2 AO, 12-bit resolution – DC 24 V supply |
Input/output card XIO11A | – 8 DI, 8 DO – DC 24 V supply |
Communication interface XFP11A | PROFIBUS IO fieldbus interface, UP TO 12 MBaud |
Communication interface XFE24A | Fieldbus interface for connection to EtherCAT networks |
XSE24A communication interface | System bus option card for expansion to EtherCAT-compatible system bus SBusPLUS |
MOVI-PLC controller – DHE41B – DHF41B – DHR41B – UHX71AB | – MOVI-PLC advanced, Ethernet interface – MOVI-PLC advanced, Ethernet / PROFIBUS / DeviceNet™ interface – MOVI-PLC advanced, Ethernet / PROFINET/ Modbus TCP / EtherNet/IP™ interface Compact controller: – MOVI-PLC power: IEC-61131-3 programmable motion and logic controller or – CCU power: parameterizable application controller |
Engineering software MOVITOOLS MotionStudio | The MOVITOOLS MotionStudio program package allows you to conveniently start up, configure and diagnose the MOVIAXIS multi-axis system. |
Braking resistors type BW | BW series braking resistors are available for the regenerative operation of the MOVIAXIS multi- axis system. Using an integrated temperature sensor, the resistor can be protected without external monitoring. |
Line choke type ND | ND series line chokes increase the overvoltage protection of the MOVIAXIS multi-axis system. This is an important characteristic in rough industrial power supply systems, especially if the inverter is installed near a supply transformer. |
Line filter type NF | The NF line filter series is available for EMC-compliant installation according to EN 61800-3. They suppress interference emission on the line side of inverters. These line filters ensure that limit value class C1 is maintained on the supply end. |
06
6.1 Control cabinet installation
MOVIDRIVE MDR regenerative power supply units
MOVIDRIVE MDR
Can be used with product series | – MOVIDRIVE B: 0.55 – 315 kW – MOVITRAC MC07B: 5.5 – 75 kW |
Features | Energy balance Braking energy from the load cycle is no longer converted into heat energy but is fed back into the grid. Energy recovery is particularly interesting for applications with a high energy potential of lowering/ deceleration movements of the load cycle, such as gantry cranes, storage/retrieval systems or lif- ting/lowering applications. |
Regenerative power supply: For central energy supply and recovery | – Used for central energy supply and recovery to supply the connected drive inverters with energy – Several MOVIDRIVE B inverters are connected in a DC link system – Energy is exchanged between the drive axes and excess braking energy is fed back into the power supply system |
Regenerative power supply: Function as a brake module (only MDR60A0150) | – Using the regenerative power supply unit as brake module means the connected inverters are not supplied with energy but only the braking energy is fed back into the power supply system – DC link supplied via the integrated input rectifier on the drive axis – Braking energy released during the application is fed back into the power supply system – The regenerative power supply unit is selected based on the braking energy released during the application, drive inverters are selected based on the motor load -> cost-optimized overall system – Example: - Power rating of drive inverters: 30 kW - Power rating of regenerative power supply unit: 15 kW |
Advantages | – Reduced overall energy consumption – Reduced CO emissions 2 – Reduced energy costs – Cost-efficient installation – No investment in braking resistors – No braking resistors need to be installed outside the control cabinet – No heating of the environment or of the control cabinet through braking resistors – Saves control cabinet space and expenditure for ventilation |
Technical data
MOVIDRIVE type MDR.. | Connection voltage V | Power range kW | Line current IN A | Overload capacity |
MDR60A0150-503-00 Size 2 | 3× AC 380 V – 500 V | 15 | – 15 As a centralized supply and regenerative power supply unit – 22 As a brake module | – 150% for 60 s As a centralized supply and regenerative power supply unit – 37 kW for 50 s As a brake module peak braking power |
MDR60A0370-503-00 Size 3 | 37 | 66 | 150% for 60 s | |
MDR60A0750-503-00 Size 4 | 75 | 117 | 150% for 60 s | |
MDR60A1320-503-00 Size 6 | 132 – 160 | 260 (at 160 kW) | 150% for 60 s max. continuous power 125% | |
MDR61B1600-503-00 Size 7 | 160 – 315 | 250 | ||
MDR61B2500-503-00 Size 7 | 400 |
06
6.1 Control cabinet installation
Regenerative power supply for MOVIDRIVE B
Regenerative power supply: Function as a brake module
– Braking energy released during the applica- tion is fed back into the power supply system
– The regenerative power supply unit is selected based on the braking energy
– Drive inverters are selected based on the motor load
– DC link supplied via the integrated input rectifier on the drive axis
3x AC 380 – 500 V
NF… line filter option
ND... line choke
ND... line choke
MOVIDRIVE MDR60A0150-503-00
regenerative power supply unit
MOVIDRIVE MDX60B/61B ... -5_3
DC link
– Reduced overall energy consumption
2
– Reduced CO emissions
– Reduced energy costs
– Cost-efficient installation
– No investment in braking resistors
– No braking resistors need to be installed outside the control cabinet
– No heating of the environment or of the control cabinet through braking resistors
– Saves control cabinet space and expenditure for ventilation