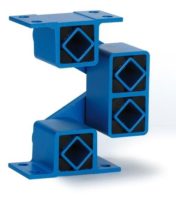
2.8
Oscillating Mountings
Technology
Design layout and evaluation
Subject
Symbol
•
Example
Unit
Mass of the empty channel and drive
m
0
680 kg
Products on the channel
200 kg
of which approx. 50 % coupling *
100 kg
Total vibrating mass *
m
780 kg
Mass distribution:
feed end
% feed end
33 %
discharge end
% discharge end
67 %
Acceleration due to gravity
g
9.81 m/s
2
Load per corner feed end
F
feed end
1263 N
Load per corner discharge end
F
discharge end
2563 N
•
Element choice in example
6 x AB 38
Working torque of both drives
AM
600 kgcm
Oscillating stroke empty channel
sw
0
8.8 mm
Oscillating stroke in operation
sw
7.7 mm
Motor revolutions
n
s
960 rpm
Centrifugal force of both drives
Fz
30’319 N
Oscillating machine factor
K
4.0
Machine acceleration
a = K · g
4.0 g
•
Natural frequency suspensions
fe
2.7
Hz
Degree of isolation
W
97 %
6.0
5.5
5.0
4.5
4.0
3.5
3.0
2.5
2.0
600
700
800
900
1000
1100
1200
1300
1400
1500
1600
1700
1800
1900
2000
2100
2200
2300
2400
2500
2600
2700
2800
2900
3000
Diagram of the
vibration isolation W [%]
* The following has to be observed for the determination of the coupling effect and material flow:
– High coupling or sticking of humid bulk material
– Channel running full
– Fully stacked screen deck with humid material
– Weight distribution with and without conveyed material
– Centrifugal force does not run through the center of gravity (channel full or empty)
– Sudden impact loading occurs
– Subsequent additions to the screen structure (e.g. additional screening deck)
•
Example
:
The proportion of the
relationship between
exciter frequency
16 Hz (960 rpm)
and mount frequency
2.7 Hz is offering a
degree of isolation
of 97%.
Calculation formulas
Oscillating machine factor
Centrifugal force
Oscillating stroke (Amplitude peak to peak)
Loading per corner
fe
n
s
90 %
92 %
94 %
95 %
96 %
97 %
98 %
99 %
sw
0
=
· 10
sw =
· 10
AM
AM
m
0
m
F
feed-end
=
m · g · % feed-end
2 · 100
F
discharge-end
=
m · g · % discharge-end
2 · 100
F
z
=
=
· n
s
· AM · 10
2 · 1000
2
π
60
n
s
2
· AM
18’240
K =
=
· n
s
· sw
2 · g · 1000
2
π
60
n
s
2
· sw
1’789’000
W = 100 –
(
)
(
)
Isolation
<
85 %
2
2
100
– 1
n
s
60
· f e
(
)
2
Vibration isolation
discharge end
conveying direction
feed end
[ mm ]
[ N ]
[ N ]
[ – ]
[ % ]