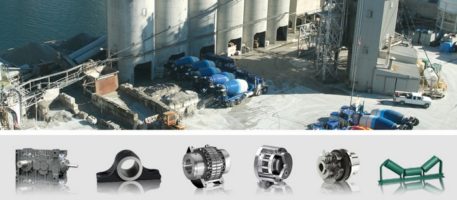

< Previous Rexnord FlatTop Chains | Products index | Next Rexnord FlatTop Chains >
Split Sprockets Injection Moulded Round Bores
Square Bores
NS 5936 T24 S40 | 614-325-4 | 24 | 40 | 147.3 | 149.2 | 25 |
The 1000-Series 1-inch pitch belt combines strong design features with an all-round pitch, making it a versatile belt; it is suitable for amongst others beverage, packaging and food industry. Mold-to-width executions are available with Positrack guiding for single line applications and packaging machines. 1000-Series can be equipped with flights for food industry applications. As a standard the belts are supplied in low friction acetal and polypropylene for beverage.
Features
• Versatile 1-inch pitch and the rigid cross-rib design result in optimum flatness and therefore superior product handling.
• The clip pin retention system in combination with the 2 module system makes the belt very easy to install and maintain.
• Rounded outside edges for better side transfers and improved product handling.
• 1000-Series belt is companioned by FTM 1060 and FGM 1050 or FT 1050 chainbelts, to make a perfect match between straight running and sideflexing conveyors.
Programme | |
1000 Flat Top (FT) | Closed surface; suitable for both glass and PET containers due to high strength. The absence of gaps prevents small (glass) particles to jam in the surface of the belt; the fully closed surface gives maximum support to the products conveyed |
1000 Flush Grid (FG) | 40% Open area; this guarantees optimum water- and airflow and allows pollution to fall through and maintain a clean con- tact surface between products and the belt. Suitable for amongst others can making and can processing |
1000 Raised Rib (RR) | 40% Open area; in combination with the special Click-Comb fingerplates the Raised Rib surface creates smooth transfers on accumulation tables, (de)palletizers and discharge tables |
1000 Raised Rib narrow (RR) | 13% Open area; suitable for packaging machines |
1000 Raised Rib Railtrack (RRR) | 1000 RR narrow belts with Railtrack, for optimum guiding and economic conveyor set-up |
1000 SuperGrip (SG) | High friction rubber surface to handle packages on inclined and declined conveyors. Standard angles up to 20° |
1000 LBP | Low Backline Pressure execution with low noise rollers, securing optimum handling of vulnerable packed products, such as shrink-wrapped trays with and without cardboard bottom |
FreeFlow | Dynamic Transfer System for complete elimination of dead plates at 90° transfers, creating self-clearing transfers |
Positrack | Lugs for accurate and reliable guiding of mass handling and single track belts, resulting in optimum product handling |
Belt accessories | Flights to handle bulk food stuff on inclined and declined conveyors; fingerplates RR 1000 and RR 1000 narrow for precise transfers |
1000-Series MatTop® Chains
Bottles conveyor with FT1000 PSX MatTop® Chain Bottles conveyor with FT1000 PSX MatTop® Chain
Assembly | Belt Type | Code Number* | Temperature range °C | Working Load (max.) | Weight | Backflex Radius (min.) | ||
Dry | Wet | N/m (21°C) | kg/m2 | mm | ||||
XLG-Acetal with Polypropylene Pins (84 has PBT pins) | ||||||||
Standard | FT 1000 XLG | 817.30.xx | 4 to 80 | 4 to 65 | 22000 | 6.50 | 25 | |
Double positrack | FTDP 1000 XLG | 873.27.xx | ||||||
Positrack 1 side, freeflow 1 side | FFTP 1000 XLG 1xP | 873.08.xx | ||||||
Positrack 2 sides, freeflow 1 side | FFTP 1000 XLG 2xP | 873.07.xx | ||||||
Double positrack 84 | FTDP 1000 XLG 84 | 873.21.09 | -30 to +80 | up to 65 | ||||
| ||||||||
Standard | FT 1000 PSX | 873.78.xx | 4 to 80 | 4 to 65 | 22000 | 6.50 | 25 | |
Double positrack | FTDP 1000 PSX | 873.79.xx | ||||||
Positrack 1 side, freeflow 1 side | FFTP 1000 PSX 1xP | 873.81.xx | ||||||
Positrack 2 sides, freeflow 1 side | FFTP 1000 PSX 2xP | 873.82.xx | ||||||
Double positrack 84 | FTDP 1000 PSX 84 | 873.79.09 | -30 to +80 | up to 65 | ||||
XP-Polypropylene with Polypropylene Pins | ||||||||
Standard | FT 1000 XP | 818.30.xx | 4 to 104 | 4 to 104 | 11000 | 4.25 | 25 | |
Double positrack | FTDP 1000 XP | 873.29.xx | ||||||
WLT-Polyethylene with Polyethylene Pins | ||||||||
Standard | WLT 1000 FT | 812.60.xx | -70 to +35 | -70 to +35 | 5000 | 4.60 | 25 | |
WHT-Polypropylene with Polypropylene Pins | ||||||||
Standard | WHT 1000 FT | 811.80.xx | 4 to 104 | 4 to 104 | 11000 | 4.30 | 25 | |
WSM-Acetal with Polypropylene Pins | ||||||||
Standard | WSM 1000 FT | 815.70.xx | 4 to 80 | 4 to 65 | 22000 | 6.50 | 25 | |
Double positrack | WSM 1000 FTDP | 873.28.xx |
1000-Series
* In code numbers xx corresponds with the belt width (A), starting with 10 for 85 mm, 11 for 170 mm and so on with 85 mm increments, or optionally 5 mm, up to 6120 mm; see also page 208.
If you need flights, describe the belt by choosing from the required options listed in the 2nd column of the table:
Material | WLT or WHT or WSM | |
Belt type | 1000 FT or 1000 FTDP | (Double) Positrack not possible for WLT, BLT and WHT |
Width (A) | KM-.. (in mm) | Belts with flights have a minimal width of 130 mm with 10 mm increments |
Flights | F3 or F2 or F1 or H.. | Standard height of 3”, 2”, 1” or special height in mm |
Pitch between flights | T..P | Flights on every ..th row (must correspond to an even number of rows) |
Flight side-indent | N.. (in mm) | Minimal 40 mm with 5 mm increments |
Example: WSM 1000 FTDP KM-430 H50 T6P N45 is a 1000 Flat Top belt with Double Positrack, made of white acetal, special width 430 mm, special 50 mm high flights on every 6th row at 45 mm from the sides
Positrack Flight 1000-series
Assembly | Belt Type | Code Number* | Temperature range °C | Working Load (max.) | Weight | Backflex Radius (min.) | ||
Dry | Wet | N/m (21°C) | kg/m2 | mm | ||||
XLG-Acetal with Polypropylene Pins (84 has PBT pins) | ||||||||
Standard | FG 1000 XLG | 817.40.xx | 4 to 80 | 4 to 65 | 22000 | 5.40 | 25 | |
Double Positrack | FGDP 1000 XLG | 874.43.xx | ||||||
Positrack 1 side, freeflow 1 side | FFGP 1000 XLG 1xP | 874.08.xx | ||||||
Positrack 2 sides, freeflow 1 side | FFGP 1000 XLG 2xP | 874.07.xx | ||||||
Double positrack 84 | FGDP 1000 XLG 84 | 874.30.09 | -30 to +80 | up to 65 | ||||
Advanced Performance Polymer Alloy with PBT pins | ||||||||
Standard | FG 1000 PSX | 874.63.xx | 4 to 80 | 4 to 65 | 22000 | 5.40 | 25 | |
Double Positrack | FGDP 1000 PSX | 874.64.xx | ||||||
Positrack 1 side, freeflow 1 side | FFGP 1000 PSX 1xP | 874.68.xx | ||||||
Positrack 2 sides, freeflow 1 side | FFGP 1000 PSX 2xP | 874.69.xx | ||||||
Double positrack 84 | FGDP 1000 PSX 84 | 874.64.09 | -30 to +80 | up to 65 | ||||
XP-Polypropylene with Polypropylene Pins | ||||||||
Standard | FG 1000 XP | 818.40.xx | 4 to 104 | 4 to 104 | 11000 | 3.53 | 25 | |
Double positrack | FGDP 1000 XP | 874.45.xx | ||||||
WLT-Polyethylene with Polyethylene Pins | ||||||||
Standard | WLT 1000 FG | 812.70.xx | -70 to +35 | -70 to +35 | 5000 | 3.70 | 25 | |
WHT-Polypropylene with Polypropylene Pins | ||||||||
Standard | WHT 1000 FG | 811.90.xx | 4 to 104 | 4 to 104 | 11000 | 3.50 | 25 | |
BHT-Polypropylene with Polypropylene Pins | ||||||||
Standard | BHT 1000 FG | 810.08.xx | 4 to 104 | 4 to 104 | 11000 | 3.50 | 25 | |
WSM-Acetal with Polypropylene Pins | ||||||||
Standard | WSM 1000 FG | 815.80.xx | 4 to 80 | 4 to 65 | 22000 | 5.40 | 25 | |
Double positrack | WSM 1000 FGDP | 874.44.xx | ||||||
SMB-Acetal with Polypropylene Pins | ||||||||
Standard | SMB 1000 FG | 810.07.xx | 4 to 80 | 4 to 65 | 22000 | 5.40 | 25 |
1000-Series
* In code numbers xx corresponds with the belt width (A), starting with 10 for 85 mm, 11 for 170 mm and so on with 85 mm increments, or optionally 5 mm, up to 6120 mm; see also page 208.
If you need flights, describe the belt by choosing from the required options listed in the 2nd column of the table:
Material | WLT or BLT or WHT or BHT or WSM or SMB | |
Belt type | 1000 FG or 1000 FGDP | (Double) Positrack not possible for WLT, BLT, WHT, BHT and SMB |
Width (A) | KM-.. (in mm) | Belts with flights have a minimal width of 130 mm with 10 mm increments |
Flights | F3 or F2 or F1 or H.. | Standard height of 3”, 2”, 1” or special height in mm |
Pitch between flights | T..P | Flights on every ..th row (must correspond to an even number of rows) |
Flight side-indent | N.. (in mm) | Minimal 40 mm with 5 mm increments |
Positrack Freeflow 1000-series
Pag. 156, 157
Pag. 156, 157
Code | Width A Temperature range °C |
Number* |
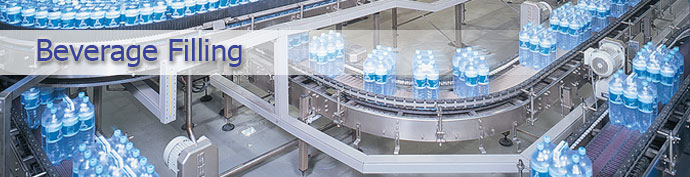
For the most demanding bottling and container applications, there is no substitute for the performance and productivity of Rexnord TableTop and MatTop Chains. Since 1938, with the ground-breaking 815 TableTop stainless steel straight-running chain, Rexnord has pioneered innovation in beverage and food conveying that has inspired loyalty and driven specification for Rexnord conveyor chains from customers around the globe.
Line efficiency
Smooth container flow at high speeds is essential to increase line efficiency and preventing product damage. Especially when moving from multiple to single lanes or the reverse, the gentle slide of bottles across ultra-flat, highly polished stainless steel Rexnord chain can contribute significantly to the quality and efficiency of your beverage production line.
Applications in beverage
Rexnord products cover a wide variety of applications like: general conveying of glass bottles one-way and return, PET bottles and other plastic containers, jars, cans 2- and 3-piece, crates, plastic containers, boxes, shrink-wrapped packages.
Product Portfolio
Rexnord offers a comprehensive of conveyor products which include
Metal TableTop chain
Plastic TableTop chain including LBP and Supergrip
Plastic MatTop chain in standard, small pitch and heavy duty alternatives.
Magnetflex Corner tracks as well as alternatives like Tab and Bevel curves
Machined and moulded sprockets
High performance polymer materials & economic alternatives for less demanding applications
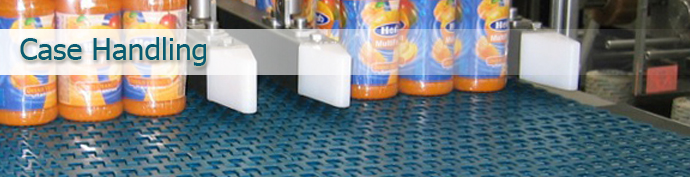
Pack and case conveying that offers flexibility of line configurations and total system cost efficiencies can significantly improve productivity at the dry end of filling lines. At the same time, brand extensions, innovative packaging, and light weight packaging materials are driving more demanding performance in pack and case handling. Cases and packs must be protected from damage even as they move rapidly out of case packers and shrink wrap machines and into, around, and out of curves.
That’s why Rexnord’s case and package handling conveying chains come in our modular small pitch, lightduty 15mm 1500 Series to medium duty 25.4mm pitch 1000 Series to the heavy-duty 1 in pitch 1005 Series in both versions for general conveying and in Super Grip / RubberTop™ versions for metering, incline, decline and braking applications. Furthermore the programm includes a comprehensive portfolio of Sideflexing MatTop chains like the versatile 1200-series MatTop. For accumulating conveyor the LBP (Low Backline Pressure) chains offers a solution to a large variety of applications.
With the Rexnord original Heavy Duty TableTop chains for packaging conveying, no other company provides the breadth of conveying solutions for your case and package handling requirements.
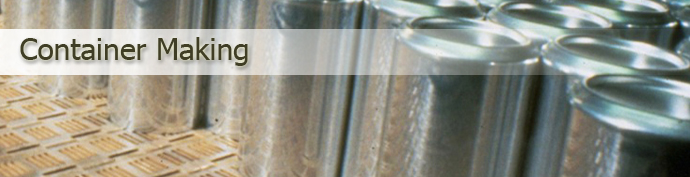
Rexnord products are known for their reliable performance in though conditions and challenging applications due to their robustness in design and drive technology. In container making therefore Rexnord products are often the preferred choice for applications like vacuum elevators, high speed (magnetic) conveyors, UV applications, high temperature applications and inspection conveyors.
Rexnord Material innovation
On top Rexnord offers the most comprehensive material portfolio in the market to meet an extensive variety of application requirements. Several applications in glassworks and container making lines combine an abrasive environment with the need for smooth container handling. Often these applications can not be easily lubricated to neutralize the effect of the hard abrasive particles in the environment. Therefore specialized materials can be part of a custom made solution. This is why, besides several proven specialized high performance materials like WX, HP and PS, Rexnords material portfolio is now completed with DKA aramid reinforced material.
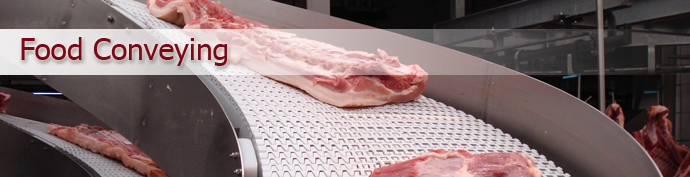
Processing and packaging food faster with a lower life-cycle cost, less downtime, and reduced product waste requires people, technology, and processes working together to make plant efficiency and productivity the number one goal.
Conveying technology in this respect is a vital part in every food processing plant. As conveying chain and components come into direct contact with food during processing, they strongly contribute to plant process hygiene. Easy-to-clean conveying chain, based on sound hygienic design, contributes to better food safety while at the same time reducing costs through more effective cleaning. Further the reliability and robustness of the chain strongly contribute to the up time of the processing line.
Rexnord food conveying chain technology and food-safe material innovations offer high productivity solutions for food applications throughout each food manufacturing plant. That is why Rexnord’s 510, 1010, 1200 and 2010 Series MatTop® Chain, with their foodgrade design and easy-to-clean features, can be an important part of a robust and effective food safety program in every food processing plant.
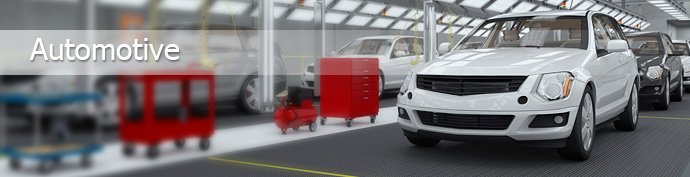
Rexnord’s automotive solutions build on more than 100 years of conveying technology experience across multiple industries. From the mechanical press to the final inspection conveyors, Rexnord has developed low maintenance modular chain solutions for your applications. By assessing your individual needs and objectives, Rexnord’s skilled engineers will help you obtain the lowest Total Cost of Ownership (TCO), resulting in significant cost savings by improving operational safety, efficiency and productivity.
Rexnord 6990 Series Hybrid MatTop Chain
The 6990 Series Hybrid MatTop Chain (patent pending) is designed for automotive conveyors with high loads or frequent load variations (people movers). The steel structure in the chain creates stiffness and strength enabling the chain to be used in conveyors with lengths over 328-feet (100m) (moving people, vehicles or a combination of the two).
Rexnord 3120 Series MatTop Chain
The 3120 Series MatTop Chain is primarily used for industrial type applications: car washes, skid handling, people movers, pallet handling, and automotive parts handling. The sturdy design is molded in high-strength acetal material and utilizes Rexnord’s Twistlock pin retention system.
Rexnord 3180 Series MatTop Chain
Rexnord recognizes the importance of opportunities to easily and economically convert from existing technology in skid applications and has developed the 3180 Series MatTop Chain. These chains are suitable for 3.2 inch (81mm) skid conveyors, allowing the skids to be aligned mechanically before transferring to the next conveyor.
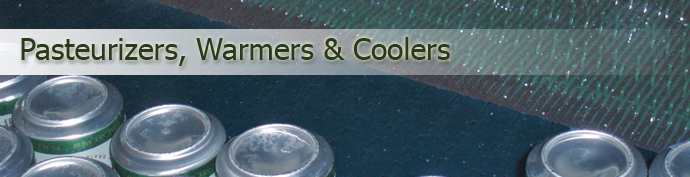
Successful processing in tunnel pasteurizers, warmers and coolers requires highly reliable, controlled conveying through the tunnel pasteurizer, and smooth container transfers at the infeed and outfeed. To have the highest conveying chain reliability, to eliminate product waste from tipped or broken containers, and to achieve durable conveying performance, Rexnord’s 2000-series USP MatTop chain and the Rexnord’s 9200 series Fortrex Stainless Steel MatTop Chain are specifically designed for superior performance in the demanding environment of pasteurizers, warmers and coolers.
DTS-C Dynamic In- and Outfeed Transfer
DTS-C patented by Rexnord combines special transfer combs and in/outfeed chains to the main Rexnord Pasteurizer belt for full self clearing transfers. This eliminates the dead plate area and ensures a continuous product flow eliminating back line pressure and potential product damage.
USP Ultra Stabilized Polypropylene Material
USP material is a unique formulation of stabilizers and anti-oxidants which protects the chain’s polypropylene material from degradation due to heat and/or chemicals. The USP material increases the reliability throughout the chain life cycle and helps to avoid the risk of unscheduled downtime.
PosiTrack centre guides
Patented integrated center guiding lugs ensure optimum chain tracking and keeps the chain sides from touching the tunnel structure, and eliminates the need to lock sprockets on the shaft.