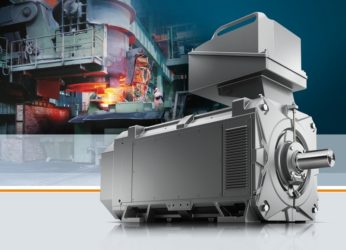
Do not hesitate to contact us! Receive immediately a full and clear answer to all your requests.
Thousands of wholesale products available. Trusted Brands. Expertise. Support.
Thousands of wholesale products available. Trusted Brands. Expertise. Support.
Competitive price from world class manufacturers for all of your MRO and production requirements.
Offering unrivalled choice, quality and value, we bring you over 50.000 individual product lines.
A team of professionals at your service to offer qualified suggestions for the most suitable products.
Do not hesitate to contact us! Receive immediately a full and clear answer to all your requests.
Tecnica Industriale Srl meet the needs of world wide customers and undertakes to respond quickly and efficiently to every needs.
We help customers save time and money by providing them the right products to keep their facilities up and running.
We offer you the highest quality products, from the world’s leading manufacturers, at the most competitive prices on the market.
The wide range of our products widely satisfy all the market’s needs in various market sectors; just one supplier to satisfy large and various operative and productive demands: our top priority is always the satisfaction of the customer.